Future Solutions

The future is innovative
HTEM300
What We Do And What We Aim For
The project aims to establish a 300-megawatt (MW) manufacturing facility for high-temperature Solid Oxide Electrolysis (SOE) stack modules, with potential future scalability towards multi-gigawatt production facilities. It also aims to completely avoid greenhouse gas (GHG) emissions relative to the reference scenario, directly contributing to Europe’s decarbonization targets and accelerating the transition from fossil fuels to clean hydrogen.
HTEM300 introduces a comprehensive and innovative approach to SOE stack module production. The project uses advanced manufacturing processes, including semi-automated assembly, quality control systems, and intelligent logistics, to ensure high production yields, consistent quality, and more effortless scalability. The SOE modules’ high operating temperature as well as the possibility to incorporate heat enables a higher electrical efficiency of 20-30% in hydrogen production compared with other technologies such as PEM electrolyzers. It allows for their installation within industrial hard-to-abate sectors with high levels of surplus heat, such as steel and fertilizer production. SOE technology’s competitive advantage and expected market growth drive further cost reductions in hydrogen production. HTEM300 aims to avoid a cumulative 3.7 million tonnes of CO₂e by replacing conventional energy carriers with renewable hydrogen.
HTEM300 aligns with the European Green Deal, the Net-Zero Industry Act and Europe’s hydrogen strategy. By fostering a domestic manufacturing ecosystem for clean hydrogen, the project contributes to Europe’s clean-tech supply chain and supports the fast and resilient scale-up of renewable hydrogen production. Developing manufacturing capacity for advanced solid oxide electrolyzer cells stack modules will reinforce Europe’s position as a global leader in green technologies and contribute to its leadership in the hydrogen sector.
The project aims to create over 100 direct and indirect jobs, contributing to the growth of the local economy and supporting the European clean-tech industry. The facility will strengthen regional supply chains and foster resilience within Europe’s clean energy infrastructure.
List of participants:
thyssenkrupp nucera HTE GmbH
thyssenkrupp nucera AG & CO. KGaA
Project coordinator
thyssenkrupp nucera HTE GmbH
Disclaimer: “Funded by the European Union. Views and opinions expressed are however those of the author(s) only and do not necessarily reflect those of the European Union or [name of the granting authority]. Neither the European Union nor the granting authority can be held responsible for them.”
Contact person:
thyssenkrupp nucera HTE GmbH
Tel.: 0231 229727100
E-Mail: info@thyssenkrupp-nucera.com
SOEC Test Facility
The Starting Position
As a leading provider of highly efficient electrolysis technologies with over 60 years of expertise in electrolysis, we are among the few global suppliers capable of producing green hydrogen on a gigawatt scale. Far from being complacent, we are constantly developing new and innovative solutions. Consequently, we view SOEC as another promising electrolysis technology deserving of investment.
Fraunhofer IKTS, a specialist in ceramic technology, has been active in the SOEC field for over 25 years and possesses comprehensive expertise across the entire value chain—from materials to systems, including economic feasibility studies. To accelerate further industrial application, collaboration is essential. This is why our strategic R&D partnership with Fraunhofer IKTS aims to advance SOEC technology for large-scale application.
What We Do
The production of green hydrogen using SOEC technology is currently confined to a laboratory and other small scale settings, indicating that we are in the early stages of developing high-temperature electrolysis for industrial-scale application. Consequently, a pilot manufacturing plant planned by Fraunhofer IKTS and operated by thyssenkrupp nucera® HTE will commence operations in the first quarter of 2025, producing high-temperature electrolysis stacks with SOE cells — the core components of SOEC stacks — in limited quantities initially. The strategic partnership also encompasses a license for thyssenkrupp nucera to produce and utilize CFY stacks based on Fraunhofer IKTS’s SOEC technology. At the pilot manufacturing plant, we are thus combining our strengths to drive forward the industrialization of SOEC technology.
What We Aim For
A further test facility will focus on validating the technology’s efficiency in converting electricity to hydrogen in the produced stacks with the use of waste heat. By conducting practical tests and economic feasibility studies, we aim to fine-tune SOEC technology for large-scale applications, ensuring it meets the high operational standards required for industrial environments. This joint effort allows us to develop solutions that seamlessly integrate into existing industrial processes. Should the initial work on industrial applications prove successful and funding be secured, we will proceed with investing in the development of large-scale production infrastructure. SOEC will be an excellent addition to our technology portfolio, providing our customers with significant benefits.
Carbon2Chem
The Starting Position
How can off-gases from steelmaking be turned into valuable precursors for fuels, plastics or fertilizers? How can we make 20 million metric tons of Germany’s steel industry’s annual CO2 emissions economically viable?
In addition to CO2, the process gases from the fully integrated steel mill also contain carbon monoxide (CO), hydrogen (H2), methane (CH4) and large quantities of nitrogen (N2), and thus the same components as synthesis gases used in the chemical industry. These are unfortunately most commonly produced from fossil resources like natural gas and crude oil. Even though steel mill off-gases and especially coke oven gas contain a lot of hydrogen, additional hydrogen is needed for synthesis of valuable chemicals.
What We Do
Our pilot plant in Duisburg is probably the only one of its kind in the world where the individual processes are practically combined and tested under industrial conditions in practical operation with real steel mill off-gases. Now for the first time, Carbon2Chem® is using these gases from the steelmaking process as a raw material for chemical production.
Moreover, to ensure that the production of the additional hydrogen required does not create a new source of CO2, it must be green: that is, produced via electrolysis from renewable energy sources and without a CO2 footprint.*
For this very purpose, an alkaline water electrolysis (AWE) plant from thyssenkrupp nucera with a capacity of 2 MW has been set up at an early stage in the pilot plant. This can run both at permanent full load as well as with rapidly changing load profiles based on the electricity market for high-quality primary control power, thus simulating the volatile availability of renewable energies, for example from wind or solar power.
What We Aim For
The partner consortium from industry and science is working together on processes for gas purification and the production of ammonia and methanol and higher alcohols. In the second funding phase, the technical processes will now be further validated, expanded towards other industries and scaled up for industrialization from 2025.
Furthermore, it has been demonstrated that the thyssenkrupp nucera AWE technology has a very good performance at both permanent full load as well as being able to follow the renewable energy profile. This finding is also systemic for the energy transition and thus of great importance beyond the actual project: Sustainable production of hydrogen via electrolysis with renewable energies is possible. The hydrogen can be produced and stored when sufficient renewable energies are available. In times of energy shortage, storage facilities can be used, making thyssenkrupp nucera’s water electrolysis an ideal upstream fit for classic industrial scale chemical processes.
*No green electricity is contracted in the Carbon2Chem Project
H2Giga
The Starting Position
How high will the demand for green hydrogen in Germany be in the future? It will amount to several million tons of hydrogen. That’s why we are involved in the hydrogen lead project H2Giga. The hydrogen lead projects are the largest research initiative to date on the topic of energy transition and supported by the German Federal Ministry of Education and Research (BMBF).
What We Do
The H2Giga project “INSTALL AWE” focuses on the industrialization of AWE, which is today the furthest developed market-ready technology and used above all for large-scale industrial applications. The modular and standardized 20 MW module from thyssenkrupp nucera is also advantageous in terms of economic aspects and climate protection.
This conserves resources and reduces the operating costs. Essential for this ramp-up to series production is the core relationship with the Joint Venture partner Industrie De Nora, a globally renowned specialist in electrochemistry and high-quality supplier for cell manufacturing and coatings.
In the H2Giga innovation pool with institutions, universities and small specialized companies offering scientific and technical skills with respect to the subject of series production, investigations of broader research and development topics are being carried out which are also intended to further drive forward our own development.
We will be receiving almost 8.5 million euros in subsidies for the research and development of the large-scale production of alkaline water electrolysis.
What We Aim For
We are driving forward the industrialization of alkaline water electrolysis (AWE) through automated series production. The aim on the one hand is to take advantage of scaling effects and thereby be able to reduce the manufacturing costs. On the other hand, an expansion of the existing supply chain of 1 GW to 5 GW of electrolysis cells enables larger project volumes to be implemented, so that several gigawatt projects can be implemented at the same time each year.
Test Facility
Gersthofen
The Starting Position
How can we ensure a continuous improvement of our bipolar membrane (BM) chlor-alkali and hydrochloric acid technologies? By trying out, testing and optimizing our technologies. In this way, we secure the control loop between suppliers and end customers and can even replicate specific customer problems to find customized solutions.
What We Do
thyssenkrupp nucera operates two test facilities each for NaCl and HCl-ODC electrolysis in production scale at the CABB site in Gersthofen. Additionally, two smaller test facilities, each for NaCl-ODC and also NaCl electrolysis in full-scale height are operated. With these facilities, we are able to develop and lift optimization potential for our electrolysis technologies, for example with regard to specific electrical power consumption. In addition to the qualification of membranes, coatings and alternative materials, designs and different operation conditions are investigated. All application cases tested in Gersthofen can be transferred without any limitation to industrial scale and thus directly to the customers’ plants.
What We Aim For
It is our goal to optimize our technologies with regard to the highest possible availability, long service life and long-term low specific electrical power consumption. We are already a global leader in chlorine technologies. But only by being close to our customers and guaranteeing them continuous improvement of our technologies we can realize our vision of being the number one in chlorine technologies.

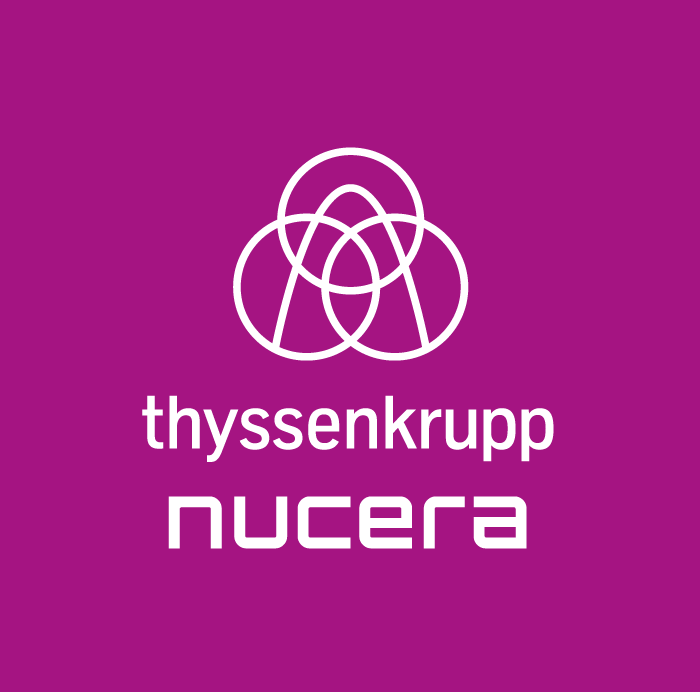